|
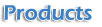 |
|
|
|
|
|
What is MIO ? |
|
|
|
|
|
Micaceous Iron oxide (MIO) is a crystalline form of iron oxide that differs from Red, Yellow, and Brown variety of iron oxides. Its crystals are very easily fractured into thin flakes & looks like mica. This similarity gives rise to the term MICACEOUS and it is normally dark grey to black in colour. All MIO ores are generally occurred in Lamellar formation, along with Non Lamellar Hematite cavities. |
|
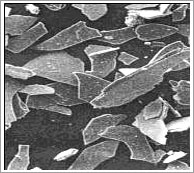 |
|
Morphology of LAMOX MIO : |
|
|
|
|
|
LAMOX is processed, Micaceous hematite ore with a metallic lustre or sparkle that can be easily seen with the naked eye. Like the other forms of iron oxide, LAMOX is a chemically inert material and is insoluble in water, organic solvents, and alkalis. It is un-reactive to most of the chemicals and is heat stable up to it's melting point of over 1,000 C (2,700 F). LAMOX is Non-Toxic, Non-Oxidizing, Non-Corrosive & Non-Flammable. With such excellent chemical & environmental properties, it is not a surprise that it is the world’s most favoured barrier pigment for over 100 years. Formulators consider MIO to be a key weapon in their anti-corrosive arsenal. Worldwide, MIO barrier type pigment is used in performance coatings, primers, plastics and glass |
|
 |
|
|
|
LAMOX MIO barrier pigment is manufactured by Lamox Industries,catering to major paint companies in india and overseas which manufacture Protective Coatings. Due to globalization in India and China the problem of corrosion brings substantial demand for Lamellar MIO. |
|
|
|
Protective Action : |
|
|
|
|
|
MIO has widespread use in protective coatings around the world because of its anti-corrosive properties, which stem from the unique nature of its flake-like particles. When MIO is incorporated into a coating system at an appropriate level, the flakes align parallel to the substrate surface, producing a shield or barrier of overlapping plates. This alignment enhances protection by providing barrier protection, ultraviolet (UV) light absorption, film reinforcement, and increased intercoat adhesion MIO has widespread use in protective industrial and marine coatings. |
|
|
|
Barrier Effect : |
|
|
|
|
|
Because LAMOX flakes are impermeable, a physical barrier is formed that prevents the ingress of water, oxygen and ions-and thus prevents corrosion of the steel and degradation of the binder. The effect is shown in the picture on the right. This picture shows that spherical fillers do not provide barrier to the coating whereas Lamellar particles are an excellent example of protective coating.
|
|
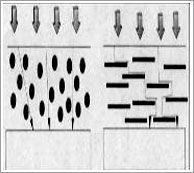 |
|
|
|
Ultraviolet Light Protection : |
|
|
|
|
|
MIO flakes are strong UV light absorbers and are very weather resistant. These properties protect the surface of the binder system from the degrading action of UV and other weathering elements. The shape and alignment of the particles permit MI0 to be much more effective than conventional granular pigments. Erosion rates and chalking are greatly reduced when MIO is present and other film properties such as flexibility are retained.
|
|
|
|
Film Reinforcement & Adhesion Promotion : |
|
|
|
|
|
Use of Lamellar Micaceous Iron Oxide flakes in a coating toughen and strengthen the film. Coatings formulated with MIO can show greatly improved resistance to blistering and increased substrate adhesion. For example, MIO is used to promote adhesion in coatings formulated for galvanized steel, around the world because of its anti-corrosive properties, which stems from the unique nature of its flake-like particles. When MIO is incorporated into a coating at an appropriate level, the flakes align parallel to the substrate surface, producing a shield or barrier of overlapping plates. This alignment enhances protection by providing harrier protection, ultraviolet (UV) light absorption, film reinforcement and increased intercoat adhesion |
|
|
|
Increased Inter-Coat Adhesion : |
|
|
|
|
|
LAMOX MIO is compatible with almost all binders but more suitable for Epoxies, that form very hard surfaces and are difficult to recoat. The incorporation of MIO produces after weathering a surface with an excellent physical profile for subsequent coats. Alternatively, coatings may be formulated with higher levels of MIO to boost the intercoat adhesion of freshly applied systems.
|
|
|
|
Coating Performance : |
|
|
|
|
|
The quality of MIO is only one of many factors that determine the performance of coating systems containing MIO. Being inert and neutral pH, are compatible with all of the major binder types. They have been used successfully in phenolics, alkyds, urethane alkyds, epoxy-esters, chlorinated rubbers, styrene acrylics (acrylated rubber), vinyl co-polymers, polyvinyl butyral resins, vinyl chloride-vinyl isobutyl ether co-polymers, epoxy resins cured with polyamines or polyamides, moisture-cured polyurethanes and two-component polyurethanes. In all cases, the protective nature of a binder will be enhanced by inclusion of an optimized level of MIO. |
|
Proper pigment loading and make-up are key to obtaining the benefits of MIO. MIO has a much lower oil absorption than other lamellar pigments. Formulations, therefore must contain much higher levels of MIO than would be the case with, for example: Silica , Talc, or Mica. The size of MIO flakes 1.5 to 2 mils long and 5-10 micrometers (0.2 to 0.4 mils) thick dictates a DFT in excess of 50 micrometers (2 mils) to achieve a shield of overlapping flakes. For this reason, MIO is normally found in high-build intermediate and finishing coats. |
|
|
|
Pigment Quality : |
|
|
|
Natural MIO is obtained from mineral deposits of specular hematite and there is tremendous variation in the physical and chemical properties of different sources and not all MIO is suitable for protective coatings. Two of the most important criteria are the amount of thin flakes and the chemical purity. These properties, however vary widely from source to source and even within a single deposit. In addition, the processing of the crude ore to remove impurities and control particle shape, size and size distribution is absolutely critical to final performance. It requires MIO pigments to have a minimum thin flake content of 60%, with a further classification into two types. Type 1 is of the highest quality with a thin flake content greater than 80%. In addition, the standard sets maximum levels for impurities and a minimum level of iron oxide content. |
|
|
|
Typical Applications of MIO Based Coating : |
|
|
|
A typical system will consist of a primer containing corrosion-inhibiting pigments; one or two coats of MIO intermediate; and, if a high gloss or bright color is required, a finishing coat based on a low chalking binder. MIO based coatings is proven technology for a coating system's durability is a proven track record on a similar structure exposed to a similar environment. Mio is a versatile pigment to make performance coating of Polyurethane, Epoxy, Acrylics, Polyesters, Alkyd, Chlorinated Rubber etc. |
|
|
|
|
|
|
|
|
|
|